Live
- Train crew suspended for violating speed limit
- Scrap NITI Aayog, bring back Planning Commission: Mamata
- Know your MLA: Satya Prabha continues husband’s legacy with resounding victory
- Dharani Revamp on Cards: CM calls for in-depth study to resolve Dharani lapses
- Huge scam in government ads
- NITI Aayog to focus on ‘Viksit Bharat @2047’
- PM playing petty politics: Oppn
- Jagan government destroyed AP economy says Chandrababu Naidu
- On Kargil Vijay Diwas, Modi hails Agnipath, targets Opposition
- War Of Words Over Kaleshwaram: Uttam accuses KTR of spreading lies
Just In
ISB alumni comes up with 'Oxyflow', made in Telangana PSA Oxygen plant
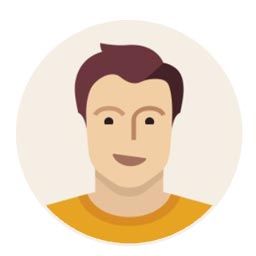
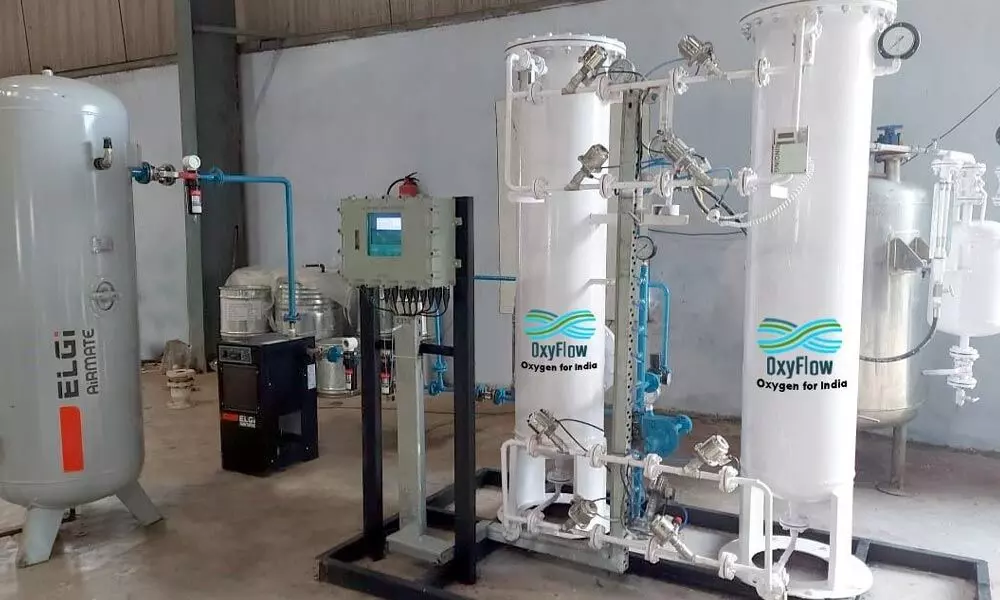
ISB alumni comes up with 'Oxyflow', made in Telangana PSA Oxygen plant
- The first plant manufactured through these contributions will be donated to a charitable hospital
- The plant produces around 60 litres of oxygen per minute with 93 per cent to 95 per cent purity
Hyderabad: A group of friends from the Indian School of Business (ISB) alumni has joined hands in designing, fabrication, and assembling an indigenous PSA Oxygen plant in Hyderabad.
Prashant Manne, CEO of Discovery Labs – a pharmaceutical manufacturing company in Hyderabad, Sireesha Yadlapalli, a senior director, The United States Pharmacopeia and Ashish Naredi, managing director of Eco Ventures and Ecotec Industries – MSME manufacturing units in Hyderabad. All of them were graduates of Class 2008 of ISB.
Speaking to The Hans India, Ashish Naredi said, "Herculean efforts are being made for expediting the oxygen supplies sourcing them from different locations in the country. One of the options to increase the oxygen supplies to the hospitals was to install Pressure Swing Adsorption (PSA) plants."
Prashant Manne, Sireesha Yadlapalli, and Ashish Naredi, classmates at ISB came together along with other friends, at the peak of the oxygen crisis to see if they could do something about the oxygen crisis. Initially, they just looked at procuring these plants and installing them at hospitals by raising funds for the same. However, all suppliers asked for a time of a minimum of six weeks for delivery which could get further extended as most of them were importing these plants to India.
That's when the friends started exploring options of manufacturing the plants in India itself. Then, they collaborated with Dr Sasidhar Gumma, from IIT Tirupati. He had been researching on the subject, and took his designs, and succeeded in operationalizing the plant in quick time. They were supported in this endeavour by their friends and families who provided the initial capital to procure the various parts and components required.
The first plant manufactured through these contributions will be donated to a charitable hospital following the wishes of all the donors, he said.The group has collaborated and assembled the plant at the manufacturing facility of Discovery labs at Choutuppal. The plant produces around 60 liters of oxygen per minute with 93 per cent to 95 per cent purity, which is the required standard for medical oxygen. At present they can manufacture around 20 plants each month with capacities of anywhere between 60 liters per minute to 1000 liters of oxygen per minute.
Prashant Mann said most of the PSA oxygen plants were being imported in light of the current oxygen crisis. The success of efforts like us indigenously manufacturing gives a big fillip not only to the availability of these plants but also to easy and cost-effective maintenance of the same. However, the key bottleneck in manufacturing these plants is the availability of a mineral called zeolite which is not found in India. The quality of zeolite (lithium-based) required for these plants had become even more scarce with the surge in demand for oxygen plants.
So, the choice was to either give up the efforts or look for alternatives. This is when the team members found another grade of zeolite (sodium-based) which was available but was not being used as it was found to be less efficient. They immediately got to work and with the help of Dr Sasidhar managed to find a way of using the lower grade (sodium-based) zeolite in the plants, without in any way compromising on either the quality or the purity of the oxygen produced. This breakthrough now made not only the manufacture of the PSA plants possible in quick time (due to easier availability of zeolite) but it also reduced the cost of the plant – both of initial setup as well as that of long-term maintenance. It took the team around 30 days to get it right but having achieved the breakthrough.
Ashish Nared said the process has three critical steps: firstly, capturing atmospheric air with the aid of an air compressor. Secondly, passing the air over a mineral called zeolite, wherein the atmospheric air is separated into nitrogen and oxygen with a process called adsorption (different from absorption). Thirdly, once nitrogen and oxygen are separated, the nitrogen is released back into the air and the oxygen is cleaned, purified, and stored for supply and use.

© 2024 Hyderabad Media House Limited/The Hans India. All rights reserved. Powered by hocalwire.com