Live
- 10 Tried-and-Tested Home Remedies for Toothaches
- Thila Taila Abhishekah Pooja to Lord Shaneswara
- Sudheer Babu’s ‘Harom Hara’ set to release on this auspicious day
- Priyanka Gandhi says BJP talking of 'tinkering' with Constitution with PM’s nod
- Vishwak Sen unveils gritty avatar as ‘Lankala Rathna’ in ‘Gangs of Godavari’ teaser
- ‘Kalki 2898 AD’ locks release date; film to entertain audience from June last week
- LS polls: PM Modi says BJP-NDA leading 2-0 after first two phases
- Plea in Madras HC seeks special polling arrangement for names 'missing' from Coimbatore voter list
- Ex CM KCR Bus tour on 4 th day
- Youth National Games 2024 kick-start in Delhi; over 5,000 athletes from 15 states vying for top honours
Just In
Sri City-based BFG India supplies parts to Vande Bharat Express
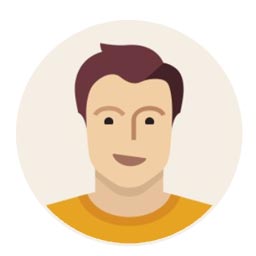
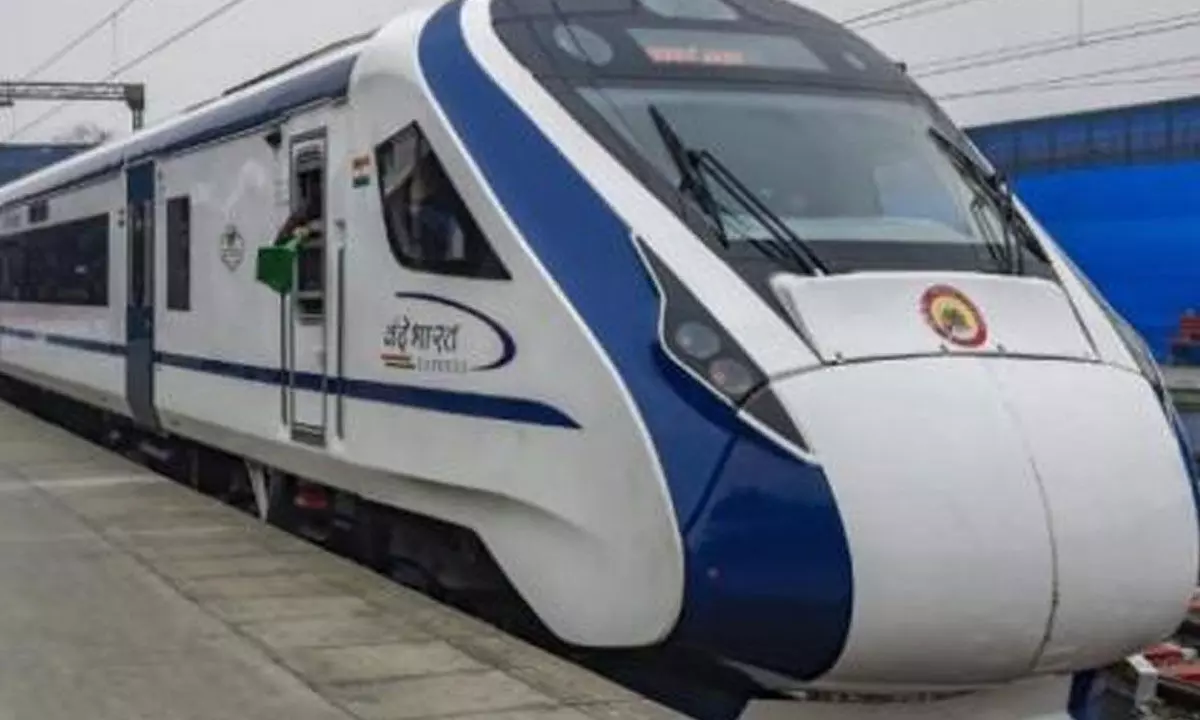
Sri City-based BFG India supplies parts to Vande Bharat Express
The subsidiary of BFG International offers world-class fibreglass reinforced plastic parts to a majority of metro rail projects in the country
Hyderabad: BFG India, a wholly owned subsidiary of BFG International, was selected to design, supply, and build the whole train interiors, toilet cabin, and front end for the Vande Bharat Express, the very first modernised train designed by ICF as part of the 'Make in India' initiative. It also offers world-class Fibreglass Reinforced Plastic (FRP) composite parts to a majority of the country's metro rail projects.
Based in the Sri City Special Economic Zone (SEZ), the company has been the region's leading manufacturer of FRP composite products and structures for a variety of industries, including wind energy, construction, transportation, and marine, since 2009. Among BFG India's notable clients are Alstom, Bombardier, Volvo, GE Energy, Gamesa, Cochin Ship Yard, Thermax, RCF, MCF and Bechtel.
Dr Ravindra Sannareddy, Founder MD of Sri City said, "It is very heartening to note that BFG's FRP products are used across different sectors, including railways." BFG India completed the given tasks in a record-breaking 10 months. In total, 329 different types of FRP panels were fabricated for the whole train. Panels of varied colours were made and integrated to meet the project's aesthetic objectives.
As part of its strategic supplier partnership with Bombardier Transportation (for Delhi metro rolling stock) and Alstom India (for the metro rolling stock of Chennai, Lucknow, Kochi, Mumbai-3, Sydney, Montreal metro projects) BFG supplies FRP parts, including interiors, front ends, driver cabs, side walls, central ceilings, lateral ceilings, gangway partitions, and cab partitions, etc.,
The front ends are made of BFG's unique phenolic material, which provides a high strength-to-weight ratio. All components meet BS-6853 fire safety requirements. BFG engineers proposed unique jigs and fixtures to handle the issues of combining FRP elements with metal parts. The hand laminated; gel coated panels manufactured met NF F 16-101 safety criteria.
Being the 'home' for numerous multinational and Indian manufacturing industries, Sri City stands out as a true manifestation of 'Make in India' campaign, in diverse industries. BFG India has a 23,600-sq m workshop here with cutting-edge facilities such as a dedicated gel coat booth with extraction system, an extensive painting facility with a pressurised spray chamber, flash off zones, and curing chambers.
Along with these, the company has an overhead crane and gantry for managing large parts, and cold storage for phenolic resins. Open contact moulding, resin transfer moulding, vacuum assisted resin transfer moulding, vacuum bagging, polyester casting, painting, systems integration, tooling machined with robotic programming and assembly are among its competences.
The superstructure for the Kochi Catamaran Ferry Water Metro Project, a pioneering project in India, was also designed by BFG. The mega-sized, infusion-made FRP superstructure is 25 metres in length, 6.5 metres in width, and 2.5 metres in height. The carrying capacity of this catamaran ferry is 100 people. The whole superstructure of the ferry was created using the vacuum infusion method.
All the interiors of the Kochi Catamaran Ferry are created in BFG's facility in Sri City before being assembled at Cochin Shipyard Ltd. BFG has obtained IRIS TS 22163 Silver Grade Certification. Also, it is an ISO-certified organisation for quality management systems.

© 2024 Hyderabad Media House Limited/The Hans India. All rights reserved. Powered by hocalwire.com