Live
- NASA Tracks Five Giant Asteroids on Close Approach to Earth Today
- Pushpa 2 Hits ₹1000 Crore in 6 Days: How It Compares to Other Top Indian Films
- Vivo X200 and X200 Pro Launched in India: Price, Specifications, and Features
- Nitin Gadkari Admits Feeling Embarrassed at Global Summits Over Rising Road Accidents in India
- Comprehensive Review on Indiramma Housing Survey and Welfare Initiatives Conducted via Video Conference
- Jogulamba Temple Records Rs 1.06 Crore Hundi Revenue in 150 Days
- Opposition Slams ‘One Nation, One Election’ Bill as Anti-Democratic; BJP Allies Support the Move
- Celebrate Karthigai Maha Deepam Virtually with Sri Mandir’s LIVE Darshan Experience
- BJP Extends Support to Samagra Shiksha Abhiyan Employees' Strike, Demands Immediate Regularization and Welfare Benefits
- Dr. M. Priyanka Stresses Quality Education, Nutritious Meals, and Cleanliness in Schools
Just In
The Trend of Liquid Silicone Rubber Injection Molding For Auto Parts Process
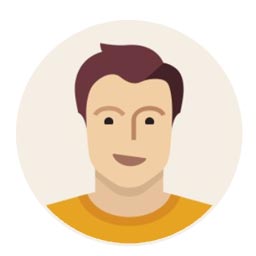
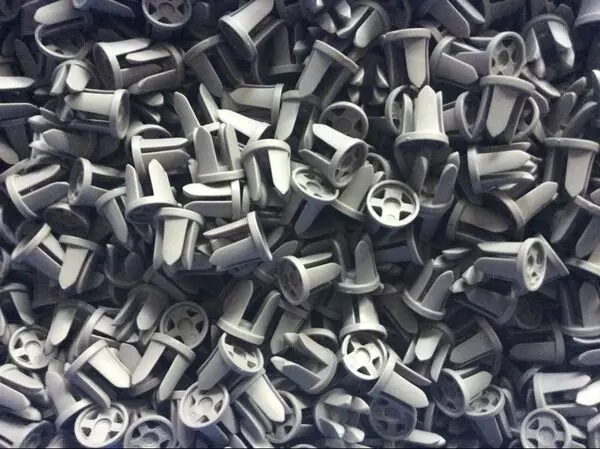
From the fastest development and stiffest competition among automakers to satisfy the customers’ thirst for long-lasting, fuel-efficient, and...
From the fastest development and stiffest competition among automakers to satisfy the customers’ thirst for long-lasting, fuel-efficient, and innovative vehicles, there is nothing surprising about it. Hence, the approach which has been very effective recently in usage of liquid silicone rubber (LSR) injection molding in producing the auto parts is seen. This article tries to highlight the rapid growth of the EV in detail through it's multi-ground benefits, various utilities, and much brighter future scope in the automotive industry.
Understand Liquid Silicone Rubber Injection Molding
What Is LSR Injection Molding?
The liquid silicone rubber shot molding process is a usage of advanced manufacturing technology whereby the high precision liquid silicone rubber material is injected into a mold cavity under high pressure. Unlike the introduced solid silicone rubber, LSR is a dual-part composition which jointly mixtured together and furthermore injected, therefore serving as a means of the prominent shape control and further properties of the resulting product. This material is injected into the form, which goes through curing process during which solidification occurs and the required part is made.
Key Features of LSR Injection Molding
High Precision: LSR injection molding is the process that facilitates themselves in the manufacture of parts with high degree of intricacy and accuracy. This capability is essential in automobiles, where small imperfections can turn into major issues with regard to performance and safety.
Chemical Resistance: LSR is the number one to resist different types of chemicals, oils and solvents widely. This makes it the most suitable choice not only for automotive parts but also other elements like important electronics and machinery.
Flexibility: LSRs' flexibility by nature allows for designing and manufacturing intricate elements that have diverse dimensions, form and geometry. This flexibility is prodigious because it makes it possible not just to produce generic but rather specially tailored components for automotive purposes as well.
Biocompatibility: LSR features the natural healthy and friendliness meaning that it can work effectively with parts that are in direct contact with the human skin and body fluids such as seals, gaskets, and medical devices used in cars.
Applications of LSR Injection Molding in Auto Parts Manufacturing
1. Seals and Gaskets
Seals and gaskets are managed as to ensuring there is no loss of engine fluids and maintaining systems such as engines, transmissions and brakes integrity. LSR injection molding is an commonly applied technique for such parts because of its excellent chemical resistance, durability, and capability to cluster up to the precision sealing walls.
2. Lighting Components
Due to hard-working tough operating conditions like a cutoff oil insulator of automobile lighting components which has to ensure not just maximal illumination and smooth operation but also durability and suitability for using in daily conditions and the weather impacts. LSR injection molding is an able substitute technology for the production of headlamp lenses, taillight seals, and other light components due to its excellent optical clarity that does not get damaged from UV rays, and has the thermal stability.
3. Electrical Connectors
With the Internet of Things set to play a large role in our near future, communication of cars and their corresponding electronic devices will require highly dependable electric connectors to ensure the smooth connection and proper functioning of these vehicles and electronic gadgets. By use of LSR injection molding, the connectors produced prove to be resistant to liquids and very stable, as well they have very good dielectric properties, so they are perfect for auto manufacturing in case of use reliability is a primary factor.
4. HVAC Components
The HVAC (heating, ventilation and air conditioning) systems have become indispensable and occupant comfort and safety facilitators in vehicles. High-flow resistance rate injection molding technology provides manufacturing for HVAC components like sealing and gaskets, which benefits from high-resistance-rate to heat and makes the automotive HVAC work more efficiency.
Advantages of LSR Injection Molding in Auto Parts Production
1. Cost Efficiency
As long as the necessary startup costs for LSR injection molding are dissipated, the method provides the best cost advantages for the car industry. It has high overall yield, quick production and process times that allow for less material wastage and decreased labor requirements, which therefore can lead to lower overall manufacturing cost over the product's lifecycle.
2. Enhanced Performance
The advantage of the shot LSR for injection molding is that it composes a superior quality finished product than those made using the traditional materials. Whether it is the increased permanence or resistance to chemicals or the improved thermal stability and flexibility, components made of LSR tend to improve the entire reliability and the product longevity.
3. Design Freedom
Another significant benefit of LSR injection molding is the capability of realizing extremely complicated feature distribution and fine designing that is usually quite difficult to be obtained by the other manufacturing procedures. Designers enjoy the supreme advantage of flexibility when making auto parts as they amend the outlook, performance, and precision of the auto parts.
4. Environmental Sustainability
LSR injection molding is an naturally friend to the environment since a greater amount of material is gotten compared to other manufacturing processes, hence wastage and energy consumption are considerably found to be low. The robustness and sustainability of LSR part design in automobiles also help by keeping the waste production to the minimum degree, thereby preventing the need of frequent substitutions.
Disadvantages of Silicone Compression Molding in Auto Parts Process
Therefore silicone injection molding has become widely used in the manufacture of automotive components because it is characterized for versatility and low acquisition cost. Nonetheless, as a production process, it is associated with a number of limitations that limit its application, and their influence must be critically evaluated. Here we discuss 3 main problems of silicone compression molding in the case of automotive industry.
1. Limited Precision and Complexity
The mention of a fact that silicone compression molding fails to produce as much accuracy and complexity as other methods like injection molding is one of the major drawbacks of silicone compression molding. Compression molding produces simple shapes and designs, but the bits of complexity masks and tight tolerances cannot be produced using this method. The drawback of autotenetics in car components is that it can sometimes lead to poorly detailed products or products with the wrong size to function properly.
2. Longer Cycle Times
The silicone compression molding normally has bigger cycle times on production lines when compared with the processes of injection molding. It is mainly screened out by the characteristics of rooting process of molding technique, where the silicon material is put into heated mold cavity and is then subjected to pressure until it is cured. This could be a case of long cycle times that can cause low production rates which may in turn slow the manufacturing efficiency and throughput.
3. Material Waste
An additional downside of silicone compression molding is the prospects of losses due to materials during the whole manufacturing process. Consecutively, compared to injection molding that specifically injects the exact amount of material in the mold cavity, compression molding is likely to leave excess material to be possibly cut or scrapped during the molding process. By doing so, it could raise material costs and bring possibilities of ignoring the wastage problem.
4. Limited Material Options
Although silicone has the positive characteristics such as flexibility, toughness and both heat and chemical resistance, the variety of materials for silicone compression molding can be considered narrow in spite of the favorable features. It can be the case that regulations on material selection, though necessary for fabrics meeting specific performance characteristics or manufacturing regulations for auto parts, nevertheless might constrain designers in their attempt of finding best available materials with respect to the set of environmental regulations. In addition, some specific resin compositions may be more difficult to press using hydroforming technologies.
5. Tooling Costs
Automobile parts usually require bespoken molds or tooling to sous isolaic molding, apart from the desired specifications. Upfront costs for tooling, however, can be a lot depending on whether the process is complex or the production is high volume. Another factor to be considered is that modifications, changes or repairs to the press tools can be needed over time thus actual costs of auto parts production using compression molding would be affected.
6. Limited Automation Potential
But the level of automation in today's manufacturing processes is much higher than ever. The processes of loading-and-unloading molds to trimming-off excess material and inspecting-finished parts have traditionally been done by hand in silicone compression molding. This fact that the manual intervention can cause variability and inconsistency in the production process cannot be shaken, especially when it comes to the high-volume manufacturing systems. Furthermore, this absence of mechanization is a barrier for this technique in widespread application on automobile parts that are needed in large quantities.
7. Surface Finish and Appearance
Silicone compression molding process, on the other hand, shows tendencies of non-uniform surface endings, compared to similar molding solutions. Facets like shape of mold, material direction, and curing state can influence both the final surface texture and the appearance of the object. Some seemingly minor surface defects may not affect the functional operation of auto parts but may however affect the aesthetic value of the part and consequently customer perception.
Future Outlook and Emerging Trends
The time-to-market model of adoption of the LSR injection molding in auto parts manufacturing will keep showing an upward trend because the automotive industry continue to look for more effective, better performing, and environmentally friendly technologies. The Future set of trends are going to include the application of Industry 4.0 technologies, like automation, robotization, and digitalization to achieve better process efficiency and quality of products.
In addition, innovative developments in LSR material creation and polymer processing technologies will also broaden the horizons for implementation of LSR injection molding in the auto industry. From lightweighting ventures to the creation of electric smart cars, the versatility and the performance qualities of the LSR become an absolute necessary component in the future development of the automotive amends in the 21st century.
In the end, the trend to apply the LSR to auto part manufacturing indicates an enormous stage of paradigm shift in the automotive industry. Enriched with many advantages of very high accuracy, high performance and flexibility, LSR injection molding uses these features to offer game changing solution in the auto parts production sector. This means vehicles that would be safer, efficient and environmentally sustainable.

© 2024 Hyderabad Media House Limited/The Hans India. All rights reserved. Powered by hocalwire.com